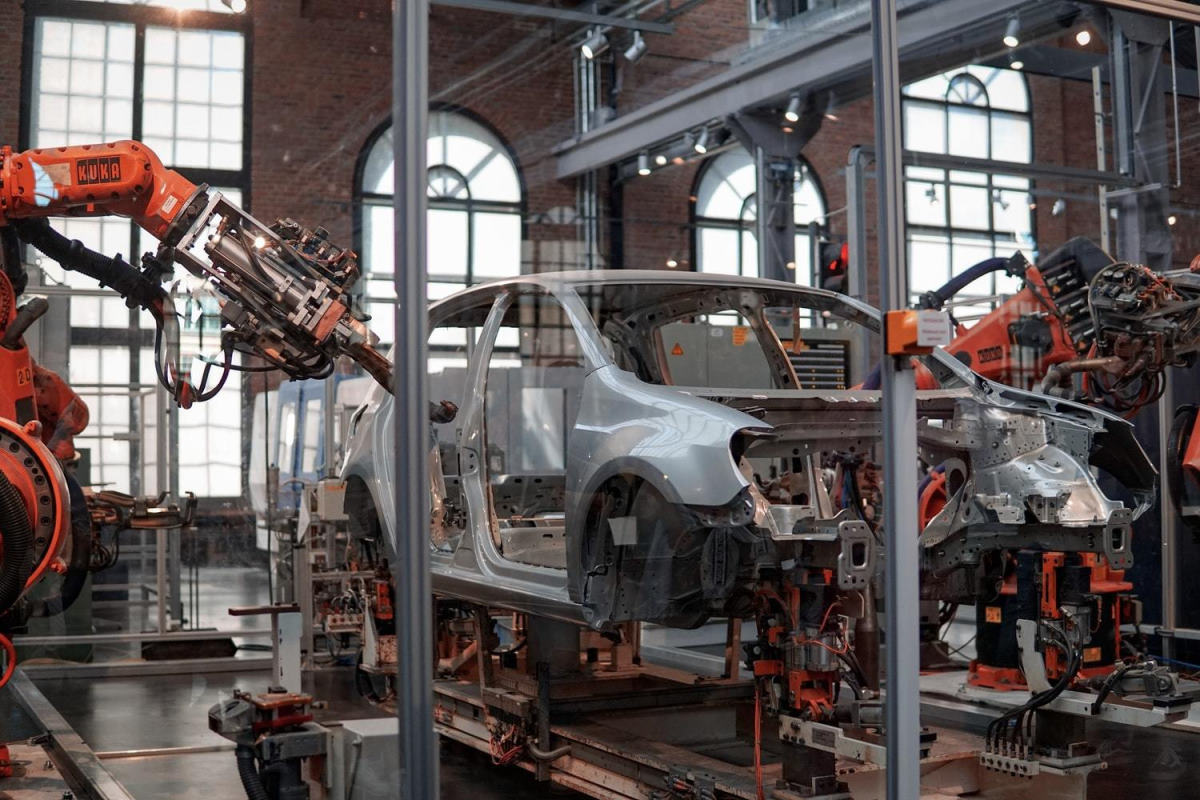
17 Jul Industry 4.0 – An Insider’s Guide
Learn about Industry 4.0 from the our team of digital factory experts.
What is Industry 4.0?
PwC defines Industry 4.0 as the focus on the end-to-end digitization of all physical assets and integration into digital ecosystems with value chain partners1.
Economic historians largely agree there were three waves of industrial revolutions:
- The first industrial revolution used water and steam power to mechanize production, an advancement from manual or animal labor used to drive production prior.
- The second industrial revolution added electricity to the mechanized production to create an era of mass production, epitomized by Henry Ford’s Model T.
- The third industrial revolution further developed on the advancement of electricity by using early robotics, computers, and other devices to further increase productivity and reduce labor costs.
The Fourth Industrial Revolution was first used by Klaus Schwab in a 2015 article in Foreign Affairs. The fourth revolution advances beyond robotics and computers, increasing productivity and quality through big data, cloud computing, machine learning, and the industrial internet of things (IIoT).
Of course, the term Industry 4.0 was invented by the Germans a few years earlier as part of a national strategy to promote digitalization of manufacturing, leveraging the internet and predictive analytics to improve productivity.
Many use the term Industry 4.0 (or I4, I 4.0) to refer to one aspect of the concept, such as a smart factory, utilizing manufacturing execution software, or the internet of things to enhance production. Those narrow uses, while accurate, are only one element of an Industry 4.0 framework.
[optin-monster-inline slug=”qloggraxd3payfghmxer”]
What are Industry 4.0 Technologies?
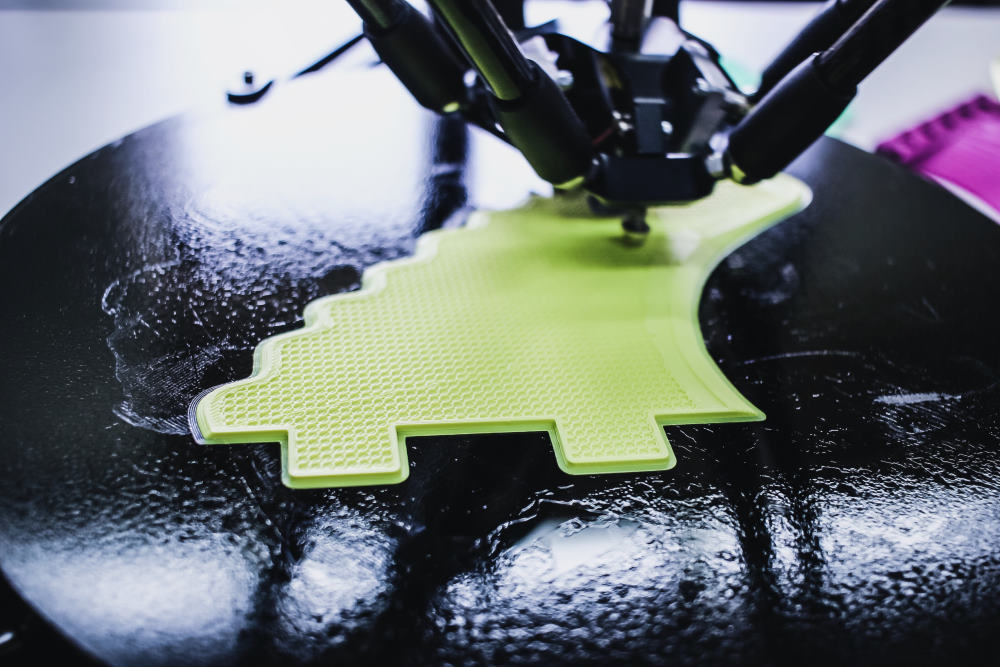
Industry 4.0 refers to more than just the technology that makes up its parts. No matter the technology or devices in use, Industry 4.0 has a couple core capabilities:
- The use of data and analytics underpins Industry 4.0. Gathering, analyzing, and sharing data across the enterprise is the entry point to leverage manufacturing technology to create more value.
- Digitization and integration of value chains where all data about operations, processes, quality management, and other key areas are available in near real-time.
Seven Industry 4.0 technologies that are revolutionizing manufacturing
- Manufacturing execution software, such as Epicor or Wonderware help you track performance across your enterprise
- Predictive analytics tools, like ABLE™ a cloud-based production line modeling tool that can predict stoppages and reports on root causes
- Cloud computing makes data available anytime, anywhere and helps integrate data across an enterprise
- Industrial Internet of Things (IIoT) connects facets of the manufacturing process to the cloud so it can be monitored, measured, and analyzed. IIoT allows for real-time analytics to be collected at the edge of your organization
- Additive manufacturing is being adopted to create quick, inexpensive prototypes and also lightweight, complicated designs for certain niche products
- Cybersecurity, authentication, and fraud detection are paramount to protect operations against cyber threats and intrusions.
- Autonomous robots and human machine interfaces (HMIs) will help humans work alongside machines in factories and warehouses
Industry 4.0 technology AT BCG’s Innovation Center AT WICHITA STATE UNIVERSITY
We’ve partnered with Boston Consulting Group to help you discover the “art of the possible.” Together with BCG, we’re showcasing our digital andon system, manufacturing analytics dashboard, and automated production line modeling software at The Innovation Center for Operations at Wichita State University’s Experiential Engineering program.
How does Industry 4.0 relate to IoT?
Often, people use Industry 4.0 and Internet of Things almost interchangeably. It is true that the Industrial Internet of Things (IIoT) is a necessary component of Industry 4.0. Adding networked sensors to manufacturing equipment is what drives the many technologies of Industry 4.0. With IIoT, companies are able to:
- Gather data from across their operation, often in real time, and use that data to improve operations.
- Understand and predict downtime and other issues with machines. Because machines are connected to a network, they can communicate important information, such as line state and line flow.
- Alert workers on the shop floor through displays and HMIs of specific issues with production.
The two issues of embracing IIoT are of security and standardization. Through IIoT you connect many disparate systems, many of which had been siloed in the past. By connecting these systems to a network, you increase the risk of cyber security risks. Also, being a new(ish) technology, there is not a single unified standard yet—OPC UA, MQTT, and PMPP. Because there is no standard it can be difficult to create one holistic data model.
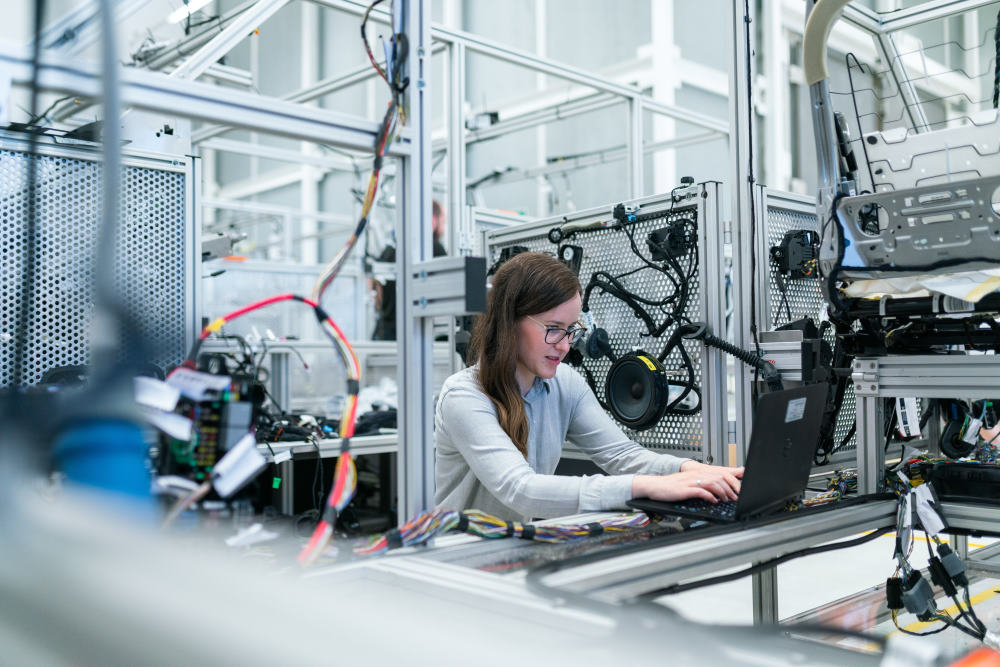
What are the challenges of implementing Industry 4.0 solutions?
Even solving the challenges mentioned above, cyber security and choosing a standard for your IIoT framework, it can still be difficult to implement such a change in your organization. Often, the barrier isn’t implementing the new technology itself, but creating a culture within your organization that embraces digital transformation and analytics.
Of course investing in the right technologies is important. However, success likely won’t hinge on what sensors you choose, the manufacturing analytics software you have, or how automated your robots are. Rather, change will need to be driven from the bottom up by hiring people fluent in digital and data, educating existing employees on new systems and practices, and communicating the value and importance of digital transformation from leadership across the organization.
What are the benefits of Industry 4.0 solutions?
In short, embracing an Industry 4.0 ethos within your organization will make your company stronger and more competitive.
If you have embraced IIoT then you can have a near omniscient view of production throughout your organization. You are also able to gather data across your organization in real time. This new capability drives many benefits throughout the organization, including:
- Improved productivity – When you are able to better understand how and where your production bottlenecks are, you can fix them.
- Decrease production costs – Through streamlined processes and improved quality management you are able to reduce costs. According to a PwC study, enterprises were able to cut expenses by 3.6% on average.
- Better resource management – With you improved data on productivity and production you are better able to plan and allocate resources across your enterprise.
- More profitability – If you are both increasing productivity and decreasing costs it isn’t hard to understand that you will increase your profit.
It’s hard to argue with profitability, however there are also some cultural benefits you may see by adopting Industry 4.0. By embracing digital technology, your organization will be able to attract young, talented workers easier. Also, with the right communication from leadership, you can instill a sense of purpose in workers that by embracing digital transformation they are making a difference in the organization. Surely a powerful sentiment to help create a culture of winning.
How can Sage Clarity help drive your Industry 4.0 strategy?
We are a manufacturing technology company delivering cutting-edge industry 4.0 solutions. Our technology has helped global companies improve their operational efficiency. Our innovative software can help your company enhance its existing infrastructure to deliver truly real-time manufacturing analytics and an enterprise-wide view of production performance.
Our suite of Industry 4.0 solutions includes:
- Enterprise Manufacturing Intelligence
- Next Generation Quality Management
- Next generation digital andon system
- One View manufacturing analytics reporting in real time
- ABLE™ Intelligent Root Cause Analysis platform
- ABLE™ Live Realtime factory visualization