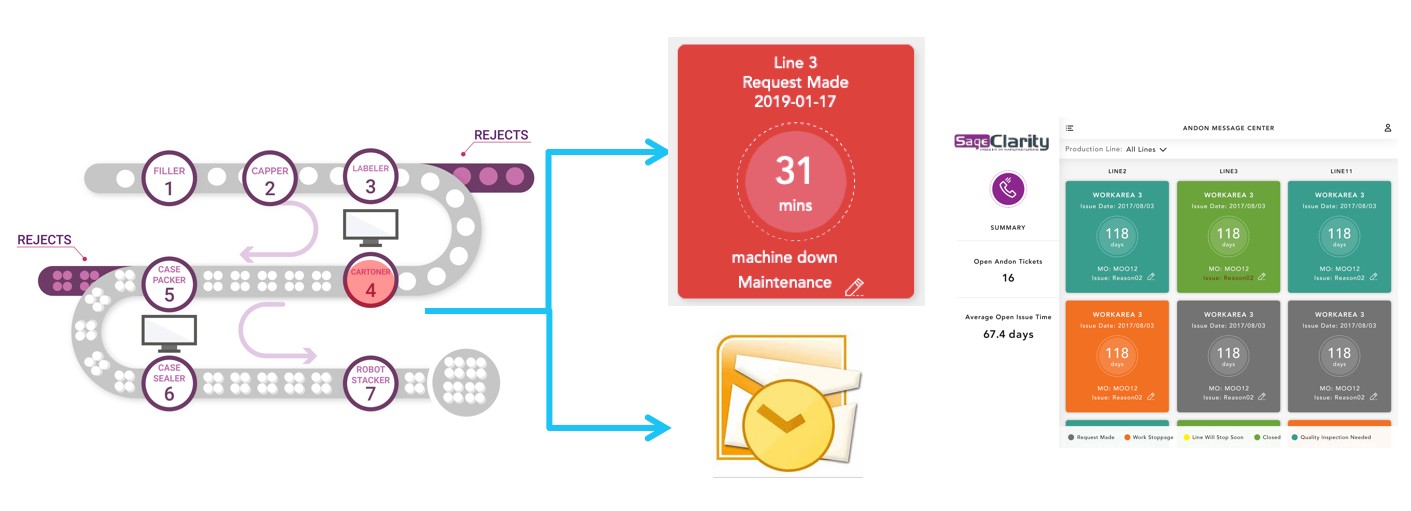
29 Apr Maximizing Efficiency: The Crucial Role of Tracking Manufacturing Minor Stops
In the realm of manufacturing, every minute counts. Efficiency isn’t just a goal; it’s the lifeblood of any successful operation. Yet, amidst the buzz of optimizing processes and streamlining workflows, there’s a small yet significant aspect that often goes unnoticed: minor stops.
These interruptions, typically lasting less than three minutes, may seem inconsequential at first glance. However, their cumulative impact on productivity and profitability can be staggering. In this blog post, we delve into the importance of tracking manufacturing minor stops and explore how doing so can drive operational excellence.
Understanding Minor Stops
Before we delve into their importance, let’s define what minor stops are. In manufacturing, minor stops refer to brief interruptions in production that are typically resolved within minutes. These pauses can result from various factors, including equipment malfunctions, material shortages, tool changes, or even brief operator interventions.
Though individually brief, minor stops can quickly add up, leading to significant downtime over time. While major breakdowns are often more visible and receive immediate attention, it’s the cumulative effect of minor stops that can erode efficiency and eat into profits unnoticed.
The Hidden Cost of Minor Stops
The impact of minor stops extends far beyond the minutes lost during each interruption. Consider the following ways in which they affect manufacturing operations:
- Reduced Overall Equipment Effectiveness (OEE): OEE is a key metric used to measure manufacturing productivity, taking into account availability, performance, and quality. Minor stops directly contribute to a decrease in equipment availability, thereby lowering overall OEE scores.
- Lost Production Time: Even though minor stops are short-lived, they disrupt the flow of production and can lead to delays in meeting production targets. This lost time can have ripple effects throughout the supply chain, affecting delivery schedules and customer satisfaction.
- Increased Maintenance Costs: Frequent minor stops can indicate underlying equipment issues that, if left unaddressed, may escalate into more significant breakdowns. Proactively addressing these issues can prevent costly repairs and downtime in the long run.
- Impact on Employee Morale: Constant interruptions can frustrate workers and disrupt their focus, leading to decreased morale and productivity. Addressing minor stops demonstrates a commitment to providing employees with a conducive work environment.
The Importance of Tracking
Given their potential impact, tracking minor stops is essential for optimizing manufacturing operations. Here’s why:
- Visibility and Awareness: Tracking minor stops provides visibility into their frequency, duration, and root causes. This awareness allows manufacturers to identify patterns and implement targeted solutions to minimize interruptions.
- Data-Driven Decision Making: By collecting data on minor stops, manufacturers can analyze trends and make informed decisions regarding equipment maintenance, process improvements, and resource allocation.
- Continuous Improvement: Continuous improvement is at the heart of modern manufacturing practices. By monitoring minor stops and implementing corrective actions, organizations can steadily enhance efficiency and drive towards operational excellence.
- Maximizing OEE: Addressing minor stops directly contributes to improving overall equipment effectiveness, thereby maximizing productivity and profitability.
Conclusion
In the fast-paced world of manufacturing, every second counts. By recognizing the importance of tracking minor stops and implementing strategies to minimize their occurrence, organizations can unlock hidden efficiencies and gain a competitive edge. Embracing a culture of continuous improvement and leveraging data-driven insights are essential steps towards optimizing manufacturing operations and achieving sustainable success.
Learn More About Sage Clarity’s Next Gen ANDON – Issue Response Accelerator