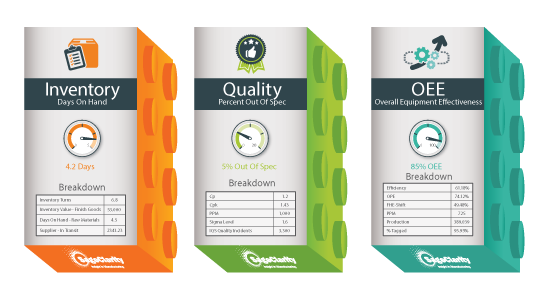
23 Feb Analytics to Improve Business Performance – What’s Real?
A recent report by LNS Research entitled The New Frontier in Manufacturing Operations and Business Performance provides strong factual evidence of how organizations can truly impact business performance by leveraging analytics. In the past year, the industry has been flooded with buzzwords such as mobility, analytics and the Internet of Things (IoT), lets boil these down to actual real business initiatives, which add value to businesses. The starting point is to understand from the executive levels of an organization the top objectives. The LNS report states: Quality, Customer Responsiveness and Increasing Capacity are the top three strategic objectives of global 2000 enterprises.
The intersection of buzzwords and business initiatives can be realized by using metric apps such as Sage Clarity’s One View – mobile analytics that provide insight in the form of key performance indicators. We then can connect multiple metric apps to provide a series of insights that aid organizations in meeting these strategic objectives.
Quality – Specifically ensuring consistent quality of products.
Figure 1: The KPI Out-of-Spec can be used effectively for improving quality consistency.
How do we make this real? Data must be analyzed not just from quality systems, but also from numerous other systems where quality can impact the supply chain. Systems such as supplier management systems, manufacturing systems and maintenance systems for example. Once we can correlate data from siloes and numerous other systems, corresponding metrics can be developed which can be measured and improved to achieve this strategic objective.
Customer Responsiveness – Responsiveness to Customer Order Demand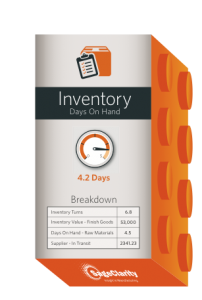
Figure 2: The KPI On-Time-In-Full (OTIF) can be a primary measure to improve responsiveness.
How does an organization enable a focus on customer responsiveness? Assuming a conventional manufacturing enterprise, and with supply chain as complex as they are, one metric which can be useful if On-Time-In-Full (OTIF). Just like quality initiatives, information for KPIs such as OTIF can be derived from numerous sources. One area to enable a culture of customer responsiveness is to propagate customer responsiveness KPIs to stakeholders in the supply chain at all levels, which can be done by leveraging a mobile analytical framework. By having KPIs that affect a customer metric available at everyone’s fingertips, each member of the team, which can impact the metric, will have the immediate knowledge of responsibilities and activities to improve the metric.
Capacity – Increasing Production Capacity & Capabilities.
Figure 3: The KPI OEE can be used to improve capacity.
Improving capacity, like the prior 2 strategic initiatives can be an entire book on its own. To make this real, we can revert back to a tried-and-true KPI of manufacturing organizations – OEE. Many organizations have embraced OEE for improving capacity. However, with mobile technologies, another way to improve OEE to the next level is using real-time analytics. While reviewing quarterly/annual performance is still a staple of improvement, having real-time access to the KPIs which affect OEE (and thus capacity) can provide knowledge-workers and executives the ability to improve capacity.
Summary
Analytics that improve business performance for supply chain organizations can be enabled by leveraging integration, mobile technologies and real-time capabilities.
[optin-monster-inline slug=”qloggraxd3payfghmxer”]