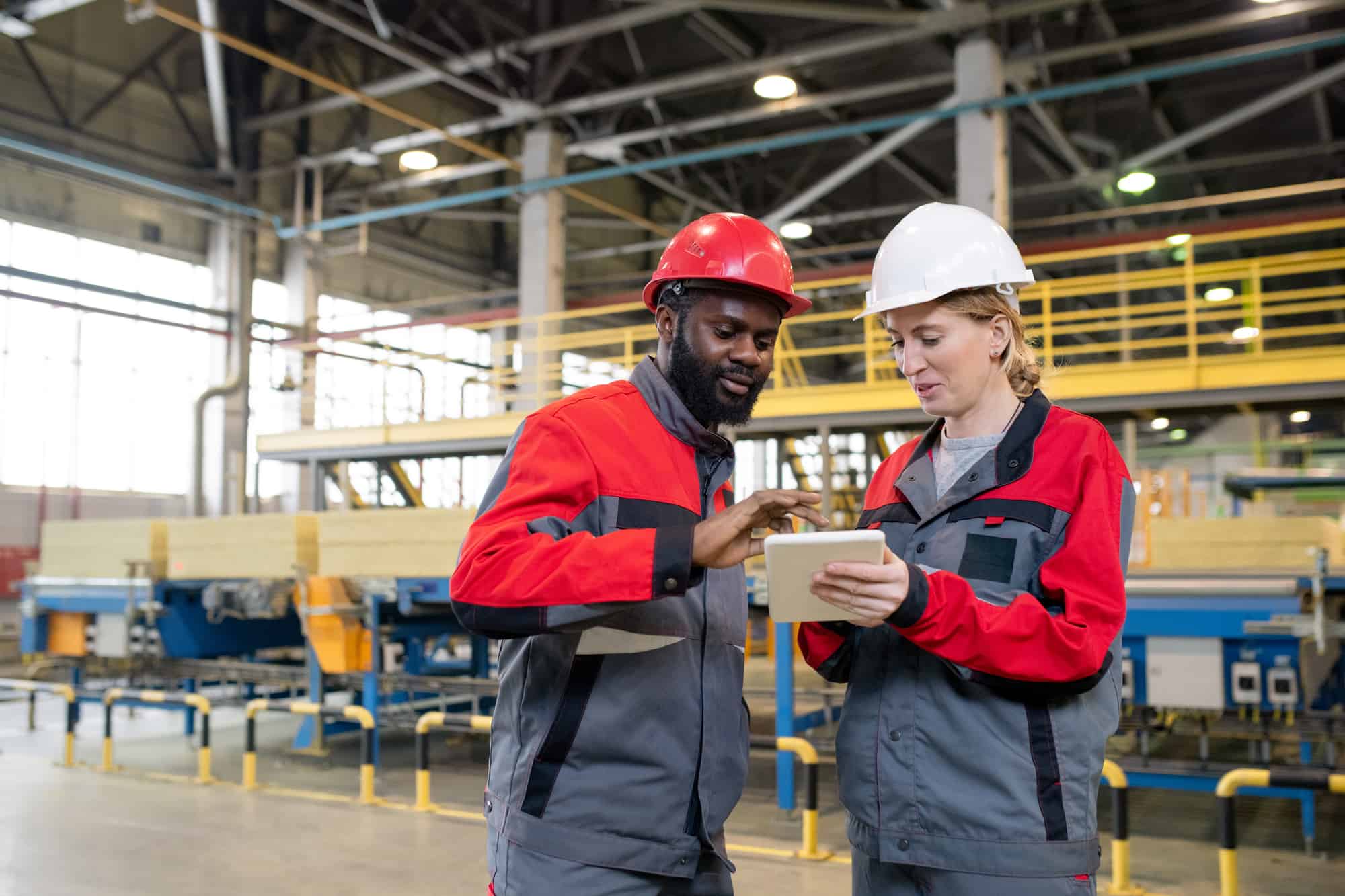
26 Apr Sage Clarity’s Equipment Asset Management (EAM) Integration: Leading-Edge Digital Approach to Maintenance Processes
Today’s manufacturers have plenty of challenges to overcome each day. From rising material and wage costs to historic labor shortages and supply chain disruptions, several obstacles can keep manufacturers from performing at peak levels to remain competitive. After all, even one simple downtime incident can cost a company up to $17,000 and up to $100,000 in certain industries.
How can manufacturers optimize their EAM investment? Sage Clarity’s Enterprise Asset Management (EAM) Integration is the answer. Using data-driven triggers, keeps maintenance costs down while optimizing the resources needed. As a result, usage-based PM activity has significant benefits over time based PM activity. By enhancing production output and optimizing assets throughout their lifespan, Sage Clarity’s EAM Integrations can help even the most traditional manufacturing companies become more efficient and competitive in today’s global marketplace.
Today’s manufacturers are increasingly moving toward digital transformation, harnessing the right technologies to maximize revenue while reducing operational costs. Read on to learn more about what Sage Clarity’s EAM does and how it can be a critical digital tool for manufacturing companies.
Prioritizing efficiency in the modern factory
OEE (Overall Equipment Efficiency) measures how efficiently a production asset operates. The associated concept of EAM (Enterprise Asset Maintenance) is the practice of planning, scheduling, and tracking the maintenance and repair of production assets. These two metrics are closely related, as EAM systems allow for monitoring performance metrics and insights that can be used to generate a full scope of asset efficiency.
In short, EAM is a complete lifecycle management solution that allows manufacturers to manage assets from procurement to scrap. Companies can expect benefits right away by implementing an EAM, including:
- A well-designed EAM system consolidates asset records, including maintenance planning, history, and spare parts inventory. With complete asset information accessible at a glance, maintenance managers can quickly determine an asset’s location, condition, and maintenance schedules and see which technicians are available to resolve any issues. An EAM streamlines maintenance on the factory floor, automating workflows to be accessible to everyone in the organization.
- Proactively resolve issues: Today’s manufacturers must take a preemptive approach to maintenance, called preventative maintenance. This strategy helps assets run more efficiently, reducing downtime and preventing costly disruptions. High-quality EAM solutions allow producers to automate preventive maintenance scheduling by performing proactive, periodic inspections that prevent machine failures and the downtime they cause.
- Minimize asset utilization: Many asset-intensive companies rely on equipment that’s decades old yet still operating, requiring parts during routine maintenance. A high-quality EAM system collects both historical and real-time data from analytical and diagnostic tools, helping producers extend the availability, reliability, and lifespan of physical assets. EAM protects these older assets that are still critical to production and costly to replace. By keeping all assets on a proactive maintenance schedule, EAM ensures peak performance of all equipment, no matter the age.
- Boost plant profitability: Preventive maintenance technologies lead to more efficient factories and intelligent manufacturing processes. Manufacturers that implement an EAM improve output, quality, and delivery, all while reducing operational costs. Well-maintained machines work better and break down less often—it’s that simple. With an EAM, manufacturers can reduce maintenance costs and downtime, boosting profitability. And when assets reach the end of their lifecycle, factory managers can expedite implementing a replacement, keeping production on track, and protecting product quality.
Super charge EAM with Sage Clarity’s solutions
Sage Clarity helps unlock the value of EAM systems by creating a digital twin of each asset’s data. The digital twin allows for enhanced visualization, real-time tracking, predictive analytics, and optimization of EAM processes. By combining EAM systems with the power of digital twinning, manufacturers can gain greater visibility into their assets and more effectively monitor performance metrics. This allows them to take proactive measures before inefficiencies are seen in data-driven insights, improving asset efficiency. Some of the key features of Sage Clarity’s EAM solution include the following:
KPI heatmaps
Maintenance managers can easily detect equipment hot spots using Sage Clarity’s KPI heatmaps, allowing them to act well in advance of costly failures. Sage Clarity’s ABLE™ technology provides intelligent root cause analysis and Machine fault learning, producing a KPI heatmap that creates unique visualizations of problematic areas in a plant. All root cause information is stored in the system’s Logic Engine, which alerts operators and managers on potential issues that could lead to equipment failure.
Using core KPIs like Availability, MTBF, and MTTR—along with real-time digital twin data—maintenance managers can determine when proactive maintenance is needed and when it’s most cost-effective to perform. Factory managers can set alerts for issues like repeat failures, excessive downtime, or workflow process deviations, taking proactive maintenance that improves OEE. Research shows companies have seen a 5-15% OEE improvement from implementing Sage Clarity’s digital solutions.
Sage Clarity’s EAM Integrations allow you to set up maintenance schedules on your timetable based on data from within your enterprise. With robust analytics and reporting, you have all the information you need to set up the most efficient, cost-effective maintenance schedule for your operation, regardless of its size or scope or even if you have multiple locations.
MES and digital twinning
Sage Clarity’s innovative ABLE™ platform actively monitors production lines, delivering real-time root cause analysis. Along with digital twins powered by IoT integrations, factory managers can detect, understand, and resolve issues at the asset level. As a result, organizations have all the tools they need to gain a real-time understanding of every piece of equipment on the factory floor, so they can make decisions about equipment that lead to a better value stream.
Organizations enjoy a fast return on investment with Sage Clarity’s EAM integrations, thanks to ABLE™’s root cause algorithm. This leading-edge technology identifies bottlenecks and producers 5-times higher data fidelity. Now, factory managers have the intelligence to reduce downtime and integration costs to manage factory assets efficiently.
OneView
Sage Clarity’s purpose-built OneView provides key insights for MES metrics. In addition, it provides a shallow dive into essential data that includes critical maintenance features like preventive maintenance, condition monitoring, work orders, inventory management, and reporting.
Thanks to OneView, factory managers can get an inside look at critical aspects of the manufacturing environment at-a-glance. Through strategic planning and monitoring, maintenance personnel can maintain critical assets based on real-time data. As a result, organizations can expect multiple benefits, like maximizing machine loading while reducing downtime, boosting efficiency with fewer maintenance tasks, and enhancing operational visibility while improving plant profitability.
Sage Clarity is the ideal digital transformation tool for manufacturers
Asset-intensive businesses, like manufacturing companies, have invested considerably in their assets and must ensure they’re getting the most from their money. EAM Integration enables efficient scheduling, monitoring, and controlling of assets. By managing how and when assets are used and analyzing the financial impact, factory managers can optimally use their assets and save on unnecessary downtime for unneeded repairs.
Ultimately, Sage Clarity’s software helps producers manage their assets more efficiently, all while reducing overall costs associated with EAM processes. Through increased visibility and predictive analytics, manufacturers can confidently streamline their EAM processes while maintaining high standards of asset efficiency.
[optin-monster-inline slug=”qloggraxd3payfghmxer”]